Ampeer Paper Subscriber Reminder
When subscribing to or renewing the paper version of the Ampeer, please make the check payable to Ken Myers. We do not have a DBA for the Ampeer or EFO. Thanks, Ken
Meaningful Naming of Outrunner Motors
Editorial Ken Myers
In last month's Ampeer, in my review of the Scorpion S-3020-11, I noted that I thought that the most meaningful way to name outrunners is by their weight in grams and Kv. I gave the example of the production Scorpion S-3014-16 compared to my special wind S-3020-11 using the same prop and battery and noted the advantages of the "heavier" motor.
If the S-3014-16 used an APC 11x7E prop (ground clearance wouldn't work on my "new" plane) so that it had about the same 307 watts input of the S-3020-11, then the drive efficiency would be down in the 69% area yielding 211.8 watts out. The RPM with the APC 11x7E would be about 7810 and the pitch speed about 14 mph less than the 3020-11 spinning the 10x8 prop at 8687 RPM.
With only a one ounce difference in the motor weights, the performance difference is quite notable, yet that "extra" one ounce would hardly be noticeable on a plane with an expected RTF weight of 40 ounces.
To further illustrate my point, here are several motors that are within one ounce of each other, therefore having about the same potential. They range in weight between ~143g/5 oz. and ~170g/6 oz. Try and use the manufacturers' and suppliers' nomenclature to find equivalent motors or any other comparisons that you might wish to do.
Atlas 2921/08, Atlas 2921/10, AXI 2820/10, AXI 2820/12, AXI 2820/14, AXI 2820/8, DualSky Xmotor 3548CA-4T, DualSky Xmotor 3548CA-5T, DualSky Xmotor 3548CA-6T, E-flite Power 15, Hacker A30-10L, Hacker A30-12L, Hacker A30-14L, Himax HC3522-0700, Himax HC3522-0990, Hyperion HP-Z-3019-10, Hyperion HP-Z-3019-12, Maxford USA Uranus-35425, NEODYM 10 NEO 10-1000, NEODYM 15 NEO 15-790, NEODYM 15 NEO 15-900, Precision Aerobatics Thrust 40, RimFire 35-48-1000, RimFire 35-48-1300, RimFire 35-48-1600, RimFire 35-48-700, RimFire 35-48-850, Scorpion 3020-12, Scorpion 3020-14, Scorpion 3020-16, Suppo 2820-06, TGY AerodriveXp SK Series 35-48 1100Kv, TGY AerodriveXp SK Series 35-48 900Kv, Torque 2814-820, TowerPro 2915-5, TowerPro 2915-6, Turnigy TR 35-48-A, Turnigy TR 35-48-B, Turnigy TR 35-48-C, Waypoint W-E3020-12, Waypoint W-E3020-14
You didn't even try, did you?
Now, let's suppose they all adopted the same naming convention of weight in grams and Kv. (Yeah, like that would ever happen!) For example, my special wind Scorpion S-3020-11 would be a Scorpion 149 - 1230.
On a spreadsheet, I renamed the same motors from above using weight in grams and the stated Kv following a dash. I sorted them by Kv and weight. That was quite an easy task. Look at this list below. Can you spot the equivalent motors? On the same battery, can you spot the one that could run the largest diameter prop? Run the smallest prop at the highest RPM? Is it easier? More importantly, is it somewhat more meaningful?
Himax 162-700
RimFire 170-700
DualSky Xmotor 165-720
TowerPro 140-750
NEODYM NEO 143.4-790
Hacker A30-14L 143-800
Turnigy 163-800
Scorpion 154-812
Torque 143-820
Precision Aerobatics Thrust 140-850
DualSky Xmotor 165-850
RimFire 170-850
AXI 151-860
Hyperion 142-900
NEODYM NEO 143-900
Turnigy 163-900
TGY AerodriveXp SK 171-900
Scorpion 154-944
TowerPro 140-950
E-flite 152-950
Waypoint 155-988
AXI 151-990
Himax 162-990
Atlas 164-990
Hacker 143-1000
NEODYM NEO 143.4-1000
Suppo 145-1000
RimFire 170-1000
Hyperion HP-Z 142-1070
DualSky Xmotor 165-1080
Scorpion 157-1088
Maxford USA Uranus 150-1100
Turnigy 163-1100
TGY AerodriveXp SK 171-1100
Waypoint W-E 155-1115
Atlas 164-1180
Hacker 143-1185
AXI 151-1200
Scorpion 149-1230
RimFire 170-1300
AXI 151-1500
RimFire 170-1600
Looking at the list above, can you pick out the motor that would be about equivalent to my special wind Scorpion 149-1230? Hopefully you see it is the AXI 151-1200. That motor is known today as the AXI 2820/10.
Since I don't expect the manufacturers and suppliers to take my advice, you can use the motor list at progressiverc.com/Brushless_Motor.html and sort the motors by weight. This page takes a while to load, but it is worth it. The data includes both in-runners and outrunners. There are links to suppliers, so that you can determine which is which if you are interested in a specific motor. Keep in mind that "much smaller" in-runners can be used in the same application as an outrunner, but they require gearing.
Knowing the weight gives us a clue as to how many watts in a motor might be used for outrunners. There is certainly room for differences of opinion about this, but in my article "One Way of Selecting a Brushless Outrunner Electric Motor for a Radio Controlled (RC or R/C) Sport Plane or Sport Scale Plane Using ANR26650M1 (A123 Systems NanophospateTM lithium ion) 2300mAh Cells", at
www.theampeer.org/M1-outrunners/M1-outrunners.htm, I previouslly used 1.5 grams of motor weight per watt in for the heaviest and 3 grams of motor weight per watt in for the lightest. I have since revised the heavier end to 1.75 grams of motor weight per watt in.
I have no experience with the NEODYM NEO 143.4-1000 (known as the NEODYM 10 NEO 10-1000) but I would say that it could be used for applications that require 250 watts in (143.3 * 1.75) to 430 watts in (143.3 * 3). When you look at my recommendation for using "A123" cells, I note that it is a good idea to use them at about 100 watts in per cell for typical sport and sport scale, fly on the wing type planes, which is about a 35 amp draw. That means that this motor could be used for 3S (300 watts in) and 4S (400 watts in) "A123" systems.
Drive Calculator does not have the Neo motor in its database, but it does the AXI 151-990 (known as the AXI 2820/12), a close enough relative. Using the AXI 2820/12 in Drive Calculator as a representative for the 1000Kv motors, I can predict what props might be usable with the Neo motor at about 35 amps.
Prop, amps, RPM and pitch speed for a 3S "A123" & Neo used as a 300 watt in motor:
APC 13x6E, 33.8 amps, 7322 RPM, 42 mph
APC 13x6 sport, 35.5 amps, 7239 RPM, 41 mph
APC 12x8E, 34.5 amps, 7288 RPM, 55 mph
APC 12x7 sport, 34 amps, 7312 RPM, 48 mph
MA 11x8 wood, 33.9 amps, 7320 RPM, 55 mph
This is the performance I'd be looking for from the unknown Neo motor. Because the Neo is slightly lighter than the AXI, and since it is a motor made in China, I really would not expect the same performance as the European AXI from Model Motors. The stated Kv of the Neo is also just slightly higher than the AXI. I would expect the amp draw to be slightly higher and RPM slightly lower, but it does get us into the ballpark.
Note that the RPM at 35 amps will always be the same no matter what prop is used and the variations seen above represent movements away from the recommended 35-amp draw. There is no need to note watts in, as it is always close to 300 for this example.
Prop, amps, RPM and pitch speed for a 4S "A123" & Neo used as a 400 watt in motor:
Aeronaut 10.5x8E, 36 amps, 9678 RPM, 73 mph
Aeronaut 10.5x7E, 33 amps, 9846 RPM, 65 mph
MA 10x8 G/F 3, 34.7 amps, 9758 RPM, 74 mph
APC 10x8 sport, 34.9 amps, 9745 RPM, 74 mph
MA 10x7 wood, 36.4 amps, 9651 RPM, 64 mph
APC 10x7E, 33.8 amps, 9812 RPM, 65 mph
Parkzone 9.5x7.5, 33.5 amps, 9833 RPM, 70 mph
APC 9x9E, 34.8 amps, 9751 RPM, 83 mph
Obviously, a NEODYM 10 NEO 10-1000 is NOT an AXI 2820/12, so what is the point? The point is that all of the motors listed with a 143g/5 oz. to 170g/6 oz. weight range with a Kv of about 1000 should perform "close" to the same. That means that the motors I have listed as the Hacker 143-1000, NEODYM NEO 143.4-1000, Suppo 145-1000, AXI 151-990, Waypoint 155-988, Himax 162-990, Atlas 164-990, and RimFire 170-1000 should all be quite close in performance using the same props and battery. Again, this demonstrates why weight in grams and Kv is a good way to name motors. It is much easier to see the relationships between them than when their manufacturers' and suppliers' names are used; Hacker A30-12L, NEODYM 10 NEO 10-1000, Suppo 2820-06, AXI 2820/12, Waypoint W-E3020-14, Himax HC3522-0990, Atlas 2921/10, and RimFire 35-48-1000.
The props listed in the 300 watts in section indicate, because of their diameter, diameter to pitch ratio and pitch speed, that the "best" application for this 1000Kv Neo, as well as the related 1000Kv motors, when using a 3S "A123" pack might be in a 2 lb./32 oz. RTF weight 3D type plane (150 watts in per pound).
The props listed in the 400 watts in section indicate that the 1000Kv motors, when paired with a 4S "A123" pack, might best be used for a "fly on the wing" 3.5 lb./56 oz. to 4.5 lb./72 oz. plane.
For my recommendations for 3S "A123" systems for sport & sport scale planes:
www.theampeer.org/M1-outrunners/M1-outrunners.htm#3CELL
For my recommendations for 4S "A123" systems for sport & sport scale planes:
www.theampeer.org/M1-outrunners/M1-outrunners.htm#4CELL
Return to "What's In This Issue"
The January EFO Meeting
The unpredictable Michigan winter weather was decent enough to allow another good turnout for the January EFO meeting held at Ken Myers' house.
Richard Utkan, EFO vice-president, showed us his all foam C-47. He had obtained plans from the Internet. It is painted using an airbrush and paint from the craft section of a Walmart store.
Jim Young brought his Wedell-Williams Model 44, which is under construction for the Scratch-Build-Off 3 on RC Groups. www.rcgroups.com/forums/showthread.php?t=969309
It is a real looker, and drew a lot of attention. Jim has designed a special latch system for holding on the wing halves for assembly at the field. It takes only moments to lock the wing halves in place.
More information on the latching system can be found in his build thread.
Keith Clark told us that Micro-Mark, the small tool specialists, have the blades for the Dremel table saw, as well as the belt. These are pretty hard to find items. Ken was especially pleased to hear this, as his saw could definitely use a new blade.
Micro-Mark has a 310 Tooth Saw Blade that is 4 inches in diameter with a 1/2-inch hole. www.micromark.com/310-TOOTH-SAW-BLADE-4-DIA-1and2-HOLE,6928.html
The 4-inch diameter 40 Tooth carbide tipped blade sounds pretty useful as well at 0.070 inches wide. www.micromark.com/40-TOOTH-SAW-BLADE-4-DIA-1and2-HOLE,7034.html
As mentioned before, they also carry the replacement belt for the Dremel table saw. www.micromark.com/REPLACEMENT-BELT-FOR-DREMEL-TABLE-SAW-ALL-MODELS,8263.html
Ken Myers showed off the new Hyperion Emeter II and RDU. He demonstrated some of the features and passed the unit around for all to inspect and ask questions about. Everyone was very impressed with this useful e-flight tool.
You can read more about the tool in the February '09 Ampeer or from a direct link on the EFO homepage.
There was a lot of information shared as the evening's snacks were downed.
Several members remembered to pay their 2009 dues, as Ken usually forgets to remind everyone. If you have not renewed your 2009 EFO membership, now would be a good time to do it.
Return to "What's In This Issue"
Hyperion Emeter II & RDU: A Closer Look
By Ken Myers
Monitoring a Battery Discharge:
01/19/09 I had a partially discharged 3S "A123" battery from the motor testing I did on my Scorpion 3020-11. I wanted to discharge it so that I could monitor a charge of the pack with the Emeter II using Zip charging.
According to version 2.07 of the manual, "In Bench-Test mode with the RDU and Emeter II connected, some actions such as accumulation of ma-h in/out and peak or minimum voltages and currents will continue even if the Emeter II is switched off. This reduces internal battery discharge rate to zero. The Emeter II will display the accumulated and peak figures from the RDU when switched on."
This made sense to me, as the RDU is what is collecting the data.
I used my AF 109 as the discharger, which takes forever, but at least it is a way that I can discharge a battery.
The screen shows that at 10:25:02 I had discharged 1181mAh. The battery was at 9.62v and the discharge had started when the pack was at 10.03v. My AF 109 on discharge is drawing 1.2 Amps. It also shows that I'm logging this part of the discharge to 008.log. I can stop the logging process by a press of the C button under the word Stop.
I did log parts of the process, but it doesn't seem that the data collected is all that valuable on battery discharge. By saving a Snapshot at the end of the discharge, that Snapshot could provide the most valuable data such as mAh Out and the starting and ending voltages.
To save a Snapshot press the D button under the word Hold. The Snapshot is then saved by pressing the C button, Save.
If the Emeter II is turned off during the test and it is logging, when it is turned back on, the RDU wants to log the data back to the Emeter SD card. Pressing Yes logs the data. I had completely cleared the log's folder before starting the record collecting. When I finished I had 9 logs.
At the end of the discharge, I took a Snapshot and saved it. I'd forgotten that the Snapshot memory is "onboard" the Emeter II, and tried to find it in the log files on the SD card. This is fine, since it can be recalled, but I would have to manually record the data, if I wanted to save it for some reason.
I expected to see the resistance of the battery pack on the BATTERY screen, but it never showed up during the discharge. A check of the manual showed that it is only displayed on the PEAKS screen.
Monitoring a Battery Charge:
During the Zip charge of the pack, I did a quick log at the beginning of the charge and another at the end to gather data that I could transfer to my Mac, instead of a Snapshot, which would have "left" the data in the Emeter II built-in memory.
To gather data for a charge, turn on the Emeter II, plug in the source to the RDU, in this case a 12v Marine/RV battery (it could have been a charger or Terminator II), start the log and then plug in the load, the battery to be charged. Stop the log after a few seconds. As the battery approaches the fully charged state, start the log again to capture the end of charge information. I had to manually stop the Zip charge, but a charger would have stopped automatically. Stop the log.
The starting log file indicated 9.72v, 24.2 amps, at 11:22:40 with an RDU temperature of 14.3-deg C. The ending log file showed 12v, 4.4 amps, at 11:33:50 with an RDU temperature of 17.3-deg C and 2084 mAh returned to the pack. It took eleven minutes and 10 seconds to charge the pack. The temperature of the RDU increased 3-deg C or 5.4-deg F during this fast charge.
I measured the "A123's" pack voltages the following morning using my Cellmeter-8 and found the cell voltages at 3.420, 3.468, and 3.379. The Astro Flight Blinky for "A123s" was connected to balance this pack, as it had not been balanced since mid-summer.
Prop Constants:
Choosing a prop from the HUGE prop database allows the Emeter II to mathematically calculate efficiency and thrust based on the prop constants in the database.
Because the prop database is so HUGE, I decided that I wanted to create a database of the props that I use most often and to add some props that I've gathered the constants for.
I checked the manual and found that the prop data is kept in a .txt file in the Data folder. The text file has fixed character lengths. The lines use this format: Name (20 characters then comma), ThrCons (7 characters with leading zeros if necessary then comma), ThrF (4 characters then comma), PwrCons (7 characters with leading zeros if necessary then comma) and PowF (4 characters).
ThrCons = Thrust Constant
ThrF = Thrust Factor
PwrCons = Power Constant
PowF = Power Factor
If you are familiar with Drive Calculator you know what these terms mean and how to derive them. If you don't understand them, the manual points you to where you can learn about them, and download more of them from the Internet.
Since this may seem a little confusing an example is presented below. I've used a / as a character place holder and it has no meaning and is not seen in the real file. It is there so that you can count the characters. I've used the APC 10x7E from the database to show what it looks like in the .txt file. There are no / in the actual APC 10x7E record. They just represent blank spaces. APC (Advanced Precision Composites) is the prop brand. TE stands for thin electric, commonly called "E" props. 1070 means a 10-inch diameter and 7-inch pitch.
Example:
Name////////////////,ThrCons,ThrF,PwrCons,PowF
--------------------------------------------
APC_TE_1070/////////,11.3670,2.15,00.2598,3.12
This is what the APC 10x7E prop looks like when displayed on the Emeter.
Since the only file that ended with .txt in the Data file folder was the prop file, I made the INCORRECT assumption that I could create a file and call 10-inch.txt and then see that as a choice in the PROP CONST menu of the Emeter II. I carefully reread the manual and learned that the Emeter II will only call a file named Props.txt. Darn! That means the original file must be saved on the computer and the new file renamed as Props.txt.
After saving the original file on my Mac with the new name orgProps.txt I saved my 10-inch.txt file as Props.txt. When I viewed the new Props.txt file, which now listed only 10-inch and 10.5-inch props, I learned that an underscore should be used as a placeholder, a space will not work.
I reworked my original 10-inch.txt file and added underscores where I wanted spaces to appear on the Emeter II screen.
This turned into an inordinately long process, as I made several mistakes that did not allow the .txt file to be displayed correctly. It took several hours, and a lot of switching the SD card from the computer to the Emeter II, and then trying again when I found my mistake. Hopefully, the software, that should be released soon, will allow an easier way to do this.
After I made a 10-inch diameter file named Props.txt, I decided to just go ahead and add all the props that I am most likely to use. I eliminated all of the folding props, APC SF props, GWS props and others that I don't use. I also added several props that I've created the constants for. Now I had a Props.txt file with just the props I use in it, which made advancing through the props with the press of the C button a lot easier!
The original Props.txt file holds 293 records. My new Props.txt file has 61 records and is much more manageable. I renamed the props in the .txt file so that they made more sense to me, as they are now what I usually call them. They now look like this:
There are also some APC pattern props and the parkzone 9.5x7.5 prop in my Props.txt file.
Here are a few props that I have the power constant and power factor for, but I do not collect thrust constants or thrust factors, therefore that data should be entered as zeros.
parkzone 9.5x7.5 PwrCons 00.2100 PowF 3.20
MA 10x7 wood PwrCons 00.3755 PowF 3.00
MA 10x8 wood PwrCons 00.4460 PowF 3.00
MA 10x8 G/F 3 series PwrCons 00.3550 PowF 3.00
MA 11x7 wood PwrCons 00.5150 PowF 3.00
MA 11x8 wood PwrCons 00.5859 PowF 3.00
APC 12x10 pattern PwrCons 00.7700 PowF 3.00
APC 12.5x10 pattern PwrCons 00.9500 PowF 3.00
APC 14x8.5E PwrCons 00.8160 PowF 3.20
Checking the Resistance of the Battery Pack:
The PEAKS screen data is only available from the "onboard" memory of the Emeter II. It must be looked at and a Snapshot taken and saved if the data is to be retrieved before the Emeter is shut off.
The pack resistance is shown on the PEAKS screen.
I used the same 3S "A123" pack that I had been using and discharged it on my AF 109. I put the Emeter II inline with the battery and discharger. At a 1.2 amp discharge the pack resistance was recorded as 0.088 Ohms or 0.029 Ohms per cell. (see above)
I charged the pack using my CellPro 10S. It said that the cell resistance in Ohms for each of the cells was 0.0092.
Once the pack was charged; I hooked it up to the motor on the test stand again. Using the ESC program that I wrote, I cycled the motor, with the prop attached as a load, several times to warm up the pack and then captured a pack Ohms reading with the Emeter II.
0.028 Ohms divided by three equals 0.0093 ohms per cell, and matches what was displayed on the CellPro 10S.
I continued to "heat things up" a bit with a few more runs, and the screen showed 0.040 Ohms for the pack.
That works out to 0.013 Ohms per cell, which would be expected as the pack heats up.
It can be seen that with the pack at about the same temperature such as it was while on the CellPro 10S and after just a few runs with the motor, the cell values are about the same.
Hyperion ATLAS and Scorpion Commander II ESC Programmer
Using version 2.08 of the firmware, the Emeter II has the ability to program Hyperion ATLAS and Scorpion Commander II ESCs.
I already had my Scorpion Commander II 45-amp ESC programmed for the motor testing of my Scorpion S-3020-11 mentioned in the February 2009 Ampeer.
I thought that I would try the new function to see just how it worked. I removed the prop from the motor on my test stand. Next I followed the directions by turning the Pot Dial to the minimum position, selecting my type ESC (15v in this case), connecting the ESC 3-pin connector to leftmost Servo Driver Port, connecting the Main Power Pack to ESC and pressing the D (Go) button.
I expected to see the settings that I had the ESC programmed to with the Scorpion IR programmer. I didn't. This is what I saw.
Next I reprogrammed the Scorpion Commander II 45-amp 15v ESC. It was quite easy to do by pressing the C button to Set my selection and the D button to go the Next menu item. When I was finished I pressed the B button to save my selections to the ESC. It took a few seconds to update the ESC with several displays on the screen and beeping from the ESC via the motor as the selections were confirmed. When I finished, I pressed the A button to Exit the programming set up. My selections were as follows.
Once again I hooked up the ESC to see if it would display my settings. It didn't.
I checked the SD card to see if the Emeter II had saved a file for this setup, and I found that it didn't.
It would be a nice feature to have the Emeter II display how the ESC is setup when it is plugged in. It would also be handy to be able to recall previous setups with one button press and have the new ESC set up like and existing one.
Power System Test Equipment that the Emeter Might Replace
Unlike a power meter, not everyone needs an Emeter II and RDU. But, if part of your enjoyment of the hobby is finding out what your power system is really doing, the Emeter II & RDU might replace many tools in your flight box.
It is not an inexpensive tool with an upfront cost of about $240 for the Emeter II, RDU, phase tachometer lead and leads for the 3 temperature sensors, but it could replace the following tools.
Power meter/wattmeter/whattmeter - ~$55.00
Optical Tachometer - ~$20.00 to $30.00
Cell Internal Resistance Meter - $50.00 - $60.00
*eLogger V3, PowerPanel LCD Display, Brushless Motor RPM Sensor, 3 Micro Temp Sensors - ~$110
Total: ~$240
*Windows computer required
As you can see, it is just about a wash, as far as the cost goes. I should note that at this time the eLogger has many more options for recording even more in-flight data. I used just the RPM sensor and 3 micro temperature sensors to keep the comparison close to the same abilities of the Emeter II as it is released. Also, the power meter and optical tachometer could be eliminated from the list, since the Eagle Tree Systems eLogger can perform the same functions.
Most of you have a computer that runs Windows; so running the eLogger software is not a problem for you. For those of us who don't use a Windows computer, the Emeter II and its RDU has a HUGE advantage.
Specifications for the Emeter II & RDU
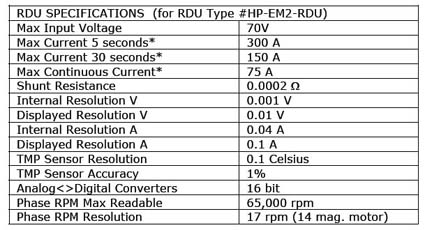
The Emeter II & RDU became available on January 26, 2009
Sources: (do a search of there site for Emeter)
http://aircraft-world.com
www.allerc.com
www.quietrcflying.com
Return to "What's In This Issue"
RCadvisor's Model Airplane Design Made Easy By Carlos Reyes Just Released

From www.rcadvisor.com/book "Build and fly your very own model airplane design. Using straightforward explanations, you will learn important design trade-offs and how to choose among them.
In this 208 page book you will discover:
When it makes sense to use one of the innovative KFm airfoils.
The latest research and techniques are explained in clear language.
The special challenges faced by the smaller models and how to overcome them.
Easy rules for selecting the right power system, both gas and electric.
Pros and cons of canard and multi-wing configurations.
How to choose the right material for each part of the airplane.
A step-by-step design process that includes goal setting and flight testing.
In-depth discussions of important topics like airfoils and wing design.
The sources of air drag and how to minimize their impact.Ó
You can read what I had to say about this book, as well as other very well known reviewers at us.rcadvisor.com/BookPreview.pdf
Return to "What's In This Issue"
|