|
Li-Poly Batteries
Where Are We Now?
Norm Dmuchowski, EFO club member, presents information on what he’s been
doing and flying with Lithium-Polymer batteries, and I try to gather some information on using them in "higher-performance"
sport and sport scale planes.
An Introduction to
Lithium-Polymer Batteries
By Norm Dmuchowski
Over the past several years I have flown slowflyer and parkflyer electric powered
planes using several generations of "lithium" formulated batteries including lithium-metal (Tadiran), lithium-ion
(Qualcomm), and now lithium-polymer (Kokam) batteries.
In 2001, I won the all up last down event at the Mid-Am using a "surplus"
2-cell 830 mAh lithium pack by Qualcomm in a Mini-Pleaser parkflyer powered by a GWS IPS - A motor. Flight times with that
setup would typically be in the 35 to 60 minute range.
With the advent of the Kokam brand lithium polymer (a.k.a. Li-Po or Li-Poly)
batteries which are safer, lighter and capable of handling higher current loads relative to their ratings, more mainstream electric
flyers are beginning to take note.
A Li-Po battery cell is charged to 4.2 volts using a charger specifically designed
for lithium-polymer cells. Each cell has a nominal voltage of 3.7 volts (as compared to 1.2 volts for Nicads). Most current
Kokam brand Li-Po batteries can safely draw three to four times their rated capacity. For example, a 1020 mAh Li-Po pack can
handle a current draw of 3-4 amps. Because of the individual cell voltage differences, flight packs of Li-Po cells for
slowflyer/parkflyer applications usually consist of only 2 or 3 cells wired in series (+ to -…). Comparable packs of Nicads or
NiMH cells which require packs of 7 to 10 cells wired in series.
Li-Po cells have a higher energy density compared to Nicads and NiMH cells
(translation: more amp capacity per ounce). A 2-cell Li-Po battery, with a capacity of 1020 mAh, is similar in power to a 7-cell
300 NiMH pack and weighs 0.4 ounces less! By substituting a 2-cell Li-Po pack for a 7-cell NiMH pack, you can get flights
three times longer, due to the higher battery capacity, and better flight performance due to the lighter battery pack weight. For
small planes, a half ounce can make a difference in flight performance.
A 2-cell 1020 mAh Li-Po pack with connector can be purchased for $27. A 7-cell
300 mAh NiMH pack with connector can be purchased for $15. To get comparable capacity and flying time, you would have to
buy 3 NiMH packs for $45. Going with Li-Po packs could save you $18. Also, chargers for Li-Po packs are comparably priced. I
recently purchased a dedicated Li-Po charger called the SC-2 from Bishop Power Products (www.b-p-p.com) which can
charge two Li-Po packs (with a maximum of three cells in series each) simultaneously at current rates up to 4.2 amps. This
charger only costs $59.95!

Li-Po packs can be charged at the field, if desired. However, I prefer to charge at
home because, unlike NiMH packs, Li-Po cells have a very low self-discharge rate, only 5% over 6 months. Thus, you can
charge your Li-Po packs several days (or weeks for that matter) ahead of time without losing significant power capacity. You
can spend your time at the field flying, rather than waiting for your NiMH or Nicad pack to peak!
Li-Po battery packs offer great flexibility in terms of meeting a wider range of
power requirements for different electric motors. Most seasoned electric flyers have an extensive inventory of packs with
different cell counts and amp capacity to meet the varied requirements of their electric motors. Li-Po packs of the same
individual cell amp capacity can be used to create whatever size pack (amp capacity and/or voltage) is required. By creatively
using battery connector adapters to put Li-Po cells into whatever series (to vary the pack’s voltage) or parallel (to vary the
pack’s amp capacity) configuration is desired, almost any configuration can be created. For example, using 1020 mAh Li-Po
cells, you could easily create a pack to handle a GWS IPS motor or a pack to handle the higher voltage or amp capacity for a
Speed 400 or a brushless motor. This can be done with as few as six 1020 Li-Po cells.

I have created two "normal" 2-cell series packs with male connectors
and created two 1-cell packs. Each 1-cell pack has two connectors. One connector is the traditional male connector and the
second connector is a female connector with the red wire connected to the negative tab of the cell and the black wire connected
to the positive tab in order to facilitate the creation of three or more cell series packs.
To create a higher voltage pack, I plug the male connector of a 2-cell pack into the
female connector of the 1-cell pack and use the male connector of the 1-cell pack as the main power connector for the newly
created 3-cell higher voltage series pack. I can continue adding as many 1-cell packs as desired in order to get the pack voltage
required.
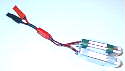
To create a higher amp capacity pack I put individual packs of the same voltage in
parallel.. To do this, I first create as many same voltage packs as I desire to put in parallel and create an adapter with multiple
female connectors wired to a single male connector (each red wire of the female connectors would be connected to the single
red wire of the male connector and do the same with the black wires). Now, I plug two 2-cell series configured 1020 mAh packs
into the female connectors of the adapter and I’ve created a pack with a 2040 mAh capacity with the same voltage as the
individual series connected packs. I can then add as many packs in parallel as needed to get to the capacity desired.
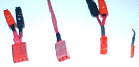
I can also combine the two 1-cell packs together to create a 2-cell series pack. To
do this, I plug a male connector of one 1-cell pack into the female connector of the other 1-cell pack. Since both 1-cell packs
have a female connector, the remaining female connector requires a male connector with both its red and black wires connected
together to form a jumper. I plug this jumper into the remaining female connector and end up with a newly created 2-cell series
pack. The remaining male connector becomes the pack’s main battery connector.
Thus with the six Li-Po cells I can create:
- two 2-cell packs and two 1-cell packs (starting setup),
- three 2-cell packs, or
- two 3-cell packs.
Combining Li-Po packs is easy to accomplish. It can also save money and the
need to have a large inventory of single purpose battery packs which we currently have with Nicads or NiMH batteries.
Li-Po battery technology is not standing still. New sizes, capacities and higher
current draw capability cells are under development and will reach the R/C electric market in the not too distant future.
Happy flying and pull up a chair because you will be spending more time in the
air!
Thank you Norm. It’s great to see EFO members contributing to the
Ampeer!
Li-Po for Powering Sport Planes
By Ken Myers
While on Winter Break in March, I decided, after hearing Norm at our February
EFO meeting, to learn more about using these cells in sport and sport scale applications. I read three articles about them;
"Lithium-Polymer Cells for R/C Flying" by James Wang, Quiet Flyer, April 2003 - Jim Zare’s "Silent Power"
column in RCM (the most helpful - Thanks JIM!), March 2003 and Cal Orr’s "Radio Spectrum" column in RCM,
March 2003.
The articles provided me with a couple of important pieces of information. When
cells are put in parallel, the to total amp draw can be safely increased. For example, the maximum amp draw on a single cell can
be up to 3C or 4C. C is the capacity of the cell, therefore the maximum amp draw for a 2070 mAh cell is 6 to 8 amps. For
higher current draws, the cells can be put into parallel configurations. Two parallel sets of the Kokam 2070 mAh cells should
safely deliver about 12 to 16 amps, 3 in parallel 18 to 24 amps and 4 in parallel 24 to 32 amps. As the cells are paralleled the
capacity also increases. For the 2070 mAh cells, 2 in parallel would have a capacity of 2070 x 2 = 4140 mAh, 3 would have 6210
mAh and 4 would equal 8280 mAh.
Next I went to the Kokam cell site at FMA Direct on the Web
(https://www.fmadirect.com/site/Products.htm?cat=28).
I got out my calculator and figured what is stated below in my question to the eflight list. At that time, I did not see the
"Calculator" on the FMA site that enables you to select the proper batteries for your electric powered models. It
either wasn’t there, or I just missed it. I then posted the following question to the eflight mailing list;
"Hi All,
Snowed in today, so I’ve been trying to learn all I can about Li-Po batteries. After
reading several articles, I still have as many questions as answers.
I want to check and see if I have this correct. I used the FMA information on the
Kokam cells to do this figuring. I believe I am TOTALLY wrong, so I’m looking for more enlightenment.
Plane: my own design low-wing TigerShark. Present power system
AF035G w/2.82:1 swinging a 10x6 MA wood prop. Static current draw 27-28 amps at the beginning of the charge. Of course
the draw goes down in flight, as I average an honest 6-8 minutes of aerobatic type flying. No it won’t hang on the prop, but
she’s a pretty good sport flier.
Right now I use 10 Sanyo 1700SCR cells, but 10 CP-1700 would do just as well
and lighten the load. Ralph Weaver gives a weight of 40g per cell, so 10 cells = 400g = 14.1 oz. for the cells. (I do believe this
weight may be too low, as I’ve also seen 1.62 oz. per cell given for these cells. But even taking 1.62 oz. per cell into account, the
following still must be wrong.)
If I’ve figured correctly, a 3S4P 2070 mAh Kokam or 3S3P 3270 mAh Kokam
pack would work. That is my first question. Did I figure this correctly?
Using the calculator that is now on the FMA Kokam site, it looks like I
did.
If my figuring is correct, then a 3S4P 2070 pack would be 12 cells times $20.50 or
$246.00 (what the calculator says is $210 - I don’t understand that) and at 44g each would weigh 528g = 18.6 oz.
for the cells. It would have a capacity of 8280 mAh, which would be equal to the capacity of 4.87 1700 mAh cells. $246 / 4.87
gives an equivalent price per pack of $50.51 for the "same" flight time as $40 (B&T Racing $4.00 per cell)
worth of CP-1700 cells. The pack weight of the Li-Po cells appears to be 4.5 ounces heavier. Where have I made my
mistake?
The 3S3P Kokam pack would be 9 cells times $30.50 or $274.50 (the
Calculator says $247 - they must be discounting a larger number of cells) and at 64g each = 576g or 20.3 oz. for the
cells. It would have a capacity of 9810 mAh or 5.77 times the 1700 mAh capacity. $274.50 / 5.77 gives an equivalent price per
pack of $47.57 for the same flight time as the $40.00 1700 mAh pack. The 3270 cell weighs 64g times 9 cells = 576 grams or
20.32 ounces, or 6.2 ounces more than a pack of CP-1700s. Again, I just can’t believe I’m doing the figuring correctly.
Would you Li-Po experts/users please give me a hand with this, so I can get a
handle on this concept? For those of you using these cells in low amp applications, please don’t respond to how well they fly
your Pico Stick, I need to know about typical sport amp draws of 25-35 amps.
A confused
Ken Myers (Walled Lake, MI USA)"
Anything in italic font above was not in the original post, but added
information since my post.
This became a "hot topic" for a few days with several posts on the
topic.
The designation 3S4P means 3 cells in series to get the required voltage and 4
three-cell packs in parallel to get the desired amp draw. The final battery, using 12 2070 mAh cells in this configuration (3S4P)
would yield a pack with a voltage of 3 cells in series times 3.7 volts = 11.1 volts, 8280 mAh and a potential amp draw of 24.84
amps (3C) to 33.12 amps (4C).
One of the first replies pointed out that since I’m getting 6 to 8 plus minutes of
flight time, my average amp draw is 13 - 17 amps. That person recommended a 3S2P pack of Kokam 3270 mAh cells. Again
that would be 11.1 volts with a capacity of 6540 mAh and a safe amp draw of 19.62 amps (3C) to 26.16 amps (4C). That seems
to make sense, since the 28+ plus amps is static on a fresh pack. This means that 6 cells would be needed to make the pack. Six
times $30.50 = $183.00 (the FMA Calculator says $165.00) and a weight of 6 times 64 g = 384 g or 13.5 oz. The weight is now
very close to the same as a 10-cell pack of CP-1700SCR cells. 6540 / 1700 = 3.85, which means that the Kokam pack would be
equivalent in flight time to about 4 packs or charges of CP-1700 Nicad cells. It is getting interesting now.
Jason Markle has been a beta tester for Thunder Power lithium cells. According
to Jason, Thunder Power cells are Japanese built Li-Po cells. He said that these cells have been working very well in higher
amperage situations. Again he mentioned the 3C and 4 C figures , but he stated that these cells can sustain a short burst of up to
8C without damaging the cells. These cells are going to be marketed by a company called Flight Energy
www.flightenergy.com
They have a capacity of 1950 mAh. He stated that he is using a configuration of
3S4P of these cells in his 10-cell planes. According to the Flight Energy site, this pack would weigh 16 ounces, again about the
same as a 10-cell CP-1700SCR pack. The capacity for this Li-Po pack would be 7800 mAh and possible amp draw between
23.4 amps (3C) and 31.2 amps (4C). That’s right in the ballpark. Unfortunately, there is no pricing available yet.
I know that these cells are working, as I’ve seen photos, taken by a friend of mine,
at the San Diego MWE meet this year. He had photos of fairly large sport and aerobatic models flying with these Thunder
Power Li-Po cells, and he told me that they were quite impressive.
Jason noted that charging is an issue, but also mentioned that the cells can be
charged in parallel at up to 1C. He said that there are few chargers at present that can charge at that rate. That would be a rate
of 7.8 amps for the pack mentioned above. He likes the Great Planes Triton charger for Li-Po cells. He stated that it can do 1-4
cells at up to 2.5 amps.
He also stated that the internal resistance of Li-Po packs is a lot lower than that of
Nicads, and that there is a very shallow discharge curve to the Li-Po cells. That means that power throughout the flight, from
beginning to end, is just about the same.
One other thing that he noted, and others such as Bernard Cawley backup, is that
the self-discharge rate of Li-Po cells is very low, so charging a week ahead of time is not a problem.
Another supplier of Li-Po cells appears to be Air Craft. They are supplying the
E-tec line of cells.
www.aircraft-world.com/prod_datasheets/lipoly.htm Air Craft
should have a charger available that will charge 1-4 cells at up to 1.5 amps by the time you read this.
The Flight Energy site has no information on chargers. FMA direct advertises a
charger for the Kokam cells that can charge 1-4 cells in series at up to 1.5 amps. Bishop Power Products has a charger that can
charge 1-3 cells at up to 4.2 amps. Tower Hobbies carries the Triton charger which can charge 1-4 cells at up to 2.5 amps.
At the time of this writing, there appears to be a "new" Kokam high
output cell arriving on the market, according to the Bishop Power Products site. There was not enough information on the site for
me to see a difference, as they were still talking about 3C to 4C sustained current with the packs they made out of 145 mAh cells,
with just a somewhat higher rise in the "burst" current into the 8C to 10C plus range. I'm still very confused about them.
The Air Craft site states that their 1200 mAh cells can sustain a discharge rate of
5C.
With all of these cells in series and parallel making up the battery, there appears to
be a problem with "cell drift". It appears that the voltage of individual cells in the pack vary greatly after several
uses and charges. There is going to have to be some way to overcome this problem.
At this time it seems we are on the cusp of being able to take several sport
aerobatic and sport scale planes to the field with Li-Po cells in them, fly several flights on each plane, and not have a charger
present. In some ways, that seems like a very good idea to me. If I obtain any further information before the time of publication
of this month’s Ampeer, I’ll be sure to present it!
A Word of Caution:
It should be noted that the Li-Po 1020 cells that Norm mentions in his article are working very
well in the applications that he’s writing about. All other uses of Li-Po cells, especially for higher performance planes are just in the beginning
stages. Very, very few modelers have used them in higher current applications, so a lot of the information presented is just speculation at this
point. Please be advised that if you try Li-Po cells in higher current aircraft, you are pioneering, and your investment may or may not be sound.
Internet Sources Mentioned in these articles:
Air Craft: www.aircraft-world.com
Bishop Power Products: www.b-p-p.com
Eflight list via the Ezone Magazine: www.ezonemag.com
Flight Energy: www.flightenergy.com
FMA direct: www.fmadirect.com
Triton Charger via Tower Hobbies: www2.towerhobbies.com/cgi-bin/wti0001p?&I=LXCJG7&P=7
Return to "What's In This Issue?"
A Simple Slow Flyer Wing
From: Lowrie McLarty jmclarty@wi.rr.com
Milwaukee, WI
Slow Flyer Under-Cambered Wings
  After being frustrated by cutting patterns for small slow flyer ribs for a Firefly
motored own design, I made a compromised airfoil using flat panels to shape a wing section. The details are attached.
  What has been irritating is the change from cutting 6" and longer symmetrical ribs to
those small ribs having under-camber. To allow undersurface film attachment most of these slow flyers ribs have many small
notches for span-wise sticks. There is not enough material left for me to get satisfactory rib shape or alignment.
  The following wing construction makes compromise rib forms as flat panels.
  This has been tried with a single surface airfoil and seems to perform well in gliding
flight. A double surface is believed possible and may be more efficient.
Advantages:
No contoured ribs or notches required.
Under-camber covering is on separate flat panels.
Wing plan form can be easily tapered.
Rib contour can be varied widely by setting panels at different angles.
Disadvantages:
Rib contour is a compromise and probably suitable only for small flyers.
A fixture may always be required to for alignment of the right and left panels.
Diagram Shows Airfoil from Side-view
Panels shown in photo below
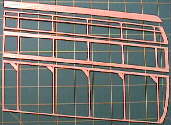
  The airfoil section shown could be closer to the ideal contour by adding longitudinal strips. The section above has only one
added strip. Strips could be added to the center panel also the trailing edge panel in order to improve the shape. A strip between
the leading edge panel and the adjacent panel would also improve the contour.
  The separate panels shown are of 1/16" Sq. medium balsa. The leading edge is soft 1/16". The center panel has
leading and trailing edges of tapered width 1/16" medium balsa. Both sides were later film covered individually before
assembling and cementing panels to each other on a simple balsa fixture.
  I’m trying to find a Milwaukee area club with big room for fragile flying.
Return to "What's In This Issue?"
Dave Grife’s 1/4-Scale "Ike" Flies
Once again, Dave sent me an email to check out the R/C Groups Discussion
thread as he had finished and flown his "Ike". The thread address is:
http://www.rcgroups.com/forums/showthread.php?threadid=74533&referrerid=1382
This is a great thread to read to learn about the evolution of a model from
conception through completion. Highly recommended reading. Here are some of the highlights. ---
"IKE" FLYS GREAT !!!!!!!!!!!
8-10 mph crosswind today, But the "Ike" flew very nicely. Loops, rolls and 4 point
rolls are all that I did today. She wanted to weather vane slightly but still a great pleasure. First flight with 4/5ths sub C's landed at
4 min. Second flight with CP-2400's landed at 6 min. I still had some electrons left after each flight. Ground handling was a bit
tricky, those gear are long! Chris Balser took some in flight photos that I hope to put up later. I'll have to get some Lithium
Polymers
"Ike" on a Hacker Today !!!!!!
The Hacker B50 11XL w/ 5.2:1 powered the "Ike" today. I used the
same prop 18-10 APC-E. The same two battery packs of 20 cells. 4/5ths sub-C's & CP-2400's.
MaxCim motor drew about 40 Amps and 5100 rpm
Hacker motor drew about 44 Amps and 5500 rpm
The Hacker motor system flew like it was running on about 4 to 6 more cells.
Flight duration turned out to be nearly identical. The Hacker motor was also significantly cooler upon flight completion.
My excitement, yesterday with the maiden "Ike" flight, was eclipsed by my
excitement with the performance today. This is the most powerful scale electric that I have ever seen.
I suspect that the MaxCim motor would have preferred that I not ended up 1.5
pounds over my initial gross weight target of 7 lbs.
I'm confident that if I altered the gear ratio and cell count w/ the MaxCim I could
get similar results.
But luckily, my 1/6th scale Howard Hughes H-1 racer is a 7 lb. airplane waiting
for a motor upgrade. New home for the MaxCim.
The "Ike" is now Hacker powered.
"Ike" Specs based on info from the thread
With MaxCim MaxN32-13Y & 20 4/5th sub-C
Wing Area: 700 sq.in. (mfg.)
Weight: 128 oz. - 8 lb.
Wing Loading: 26.33 oz./sq.ft.
Wing Span: 64 in.
MaxCim MaxN32-13Y
Wt. 7.5 oz.
Kv = 1420, Io = 0.8, Rm = 0.058
3.7:1 reducer: Wt. 2 oz.
Total Motor + reducer Wt. = 9.5 oz.
20 CP-1700 (1.62 oz.) = 32.4 oz.
Motor + reducer % of total = 7.4%
Cell weight % of total = 25.3%
Total motor + reducer + CP-1700 battery = 32.7%
Note the following mathematical estimations are based on the voltage near the
beginning of the pack discharge and apply to static testing conditions. Amp draw will decrease in the air and as the pack
discharges through the flight, but since most of us tach and test on the ground, these figures can be used for comparison.
Using 18x10E prop:
Watts in 1000 (40*1.25*20) - Watt/lb. 125
Watts to motor 764.8 - Watt/lb. 95.6
Watts to prop 658.6 - Watt/lb. 82.3
RPM 5,103
Orme’s Rule: 14 - 21 cells
Ken’s Modified Orme’s Rule: 14 - 23 cells
Flight Factor: 2.966
Diameter Factor w/ 18x10: 1.99
Pitch Factor w/ 18x10: 0.56
"Speed" to RPM Factor w/ 18x10: 2.69
With Hacker B50 11XL & 20 CP-2400
Wing Area: 700 sq.in. (mfg.)
Weight: 140.8 oz. - 8.8 lb.
Wing Loading: 29 oz./sq.ft.
Wing Span: 64 in.
Hacker B50 11XL
Wt. 11.7 oz.
Kv = 1435, Io = 1.12, Rm = 0.0152
5.2:1 reducer: Wt. 2 oz.
Total Motor + reducer Wt. = 13.7 oz.
20 CP-2400 (2.05 oz.) = 41 oz.
Motor + reducer % of total = 9.7%
Cell weight % of total = 29.1%
Total motor + reducer + CP-1700 battery = 37.4%
See note above about mathematical estimations used for comparison.
Using 18x10 prop:
Watts in 1100 (44*1.25*20) - Watt/lb. 125
Watts to motor 889 - Watt/lb. 101
Watts to prop 837.7 - Watt/lb. 95.2
RPM 5,529
Orme’s Rule: 14 - 21 cells
Ken’s Modified Orme’s Rule: 14 - 23 cells
Flight Factor: 3.262
Diameter Factor w/ 18x12: 1.81
Pitch Factor w/ 18x12: 0.56
"Speed" to RPM Factor w/ 18x12: 2.78
If you look at the prop watts on both motor setups you will see that the Hacker is
837 watts out and the MaxCim is 658.6. That is a difference of 178.4 watts out. At the end of the thread Dave states,
"The Hacker motor system flew like it was running on about 4 to 6 more cells. Flight duration turned out to be nearly
identical. The Hacker motor was also significantly cooler upon flight completion." What a great observation, since the
Hacker motor is putting out about the equivalent of 4 more cells at this amp draw!
The only thing that I can’t figure out is how the planetary gearbox on the MaxCim
is a 3.7:1 ratio, since both motors have about the same Kv and Io, with the MaxCim having about 3.8 times the resistance of the
Hacker, I expected the gear ratios to be closer to each other in ratio. The motor RPM for the MaxCim at 40 amps should be
about 23,800 and with about 5,100 RPM at the prop, the gear ratio figures closer to 4.7:1.
Another way to look at this problem is that at 5,100 RPM and with a gear ratio of
3.7, that yields a motor RPM of 18,870. With a Kv of 1420 that means that the motor "is seeing" 13.3 volts. At 40
amps and a Rm of 0.058 the "volt loss" equals 2.32 volts. The volts to the motor then equal only 15.62 volts, and with
20 cells, even at 40 amps, it should still be closer to 19 volts. That’s a head scratcher.
Great plane Dave. I can’t wait to see it fly.
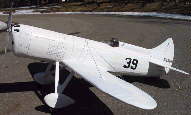
Return to "What's In This Issue?"
NIRAC
(NATIONAL INDOOR REMOTE-CONTROLLED AIRCRAFT COUNCIL)
COMPETITION NOTICE
FIRST ANNUAL INDOOR R/C CHAMPIONSHIP
DATES: Saturday May 31, 2003
And Sunday, June 1, 2003
Location: Oakland Yard, Waterford, Michigan
(approx. 100 miles north of Toledo, northwest of Detroit and just east of the Pontiac
International Airport)
Facility Size: 240 X 300 feet, with an 82 feet ceiling
Contest Director: Dave Robelen @ aplusfarm@hovac.com
Events: 6 events planned, with trophies to third place
An overall high point Championship Award
Individual Event rules and a registration form can be found on the NIRAC website:
www.nirac.org
Hobby Vendors will be selling on-site
Information on local lodging and a Saturday night banquet can be
obtained from John Worth @ johnworth@cox.net
General information available from NIRAC President
Bob Wilder @ rjwmaw5@attbi.com
And NIRAC Vice President
Bob Aberle @ baberle@optonline.net
Pre-Registration is recommended!
Return to "What's In This Issue?"
Get Mid-Am 2003 at this page.
Return to "What's In This Issue?"
To Reach Ken Myers, you can land mail to the address at the top of the page. My E-mail
address is:
KMyersEFO@aol.com
EFO WEBsite: http://members.aol.com/KMyersEFO/
|
|